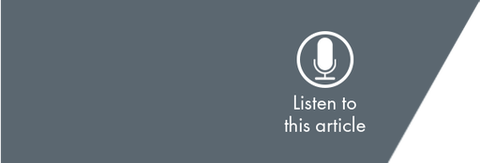
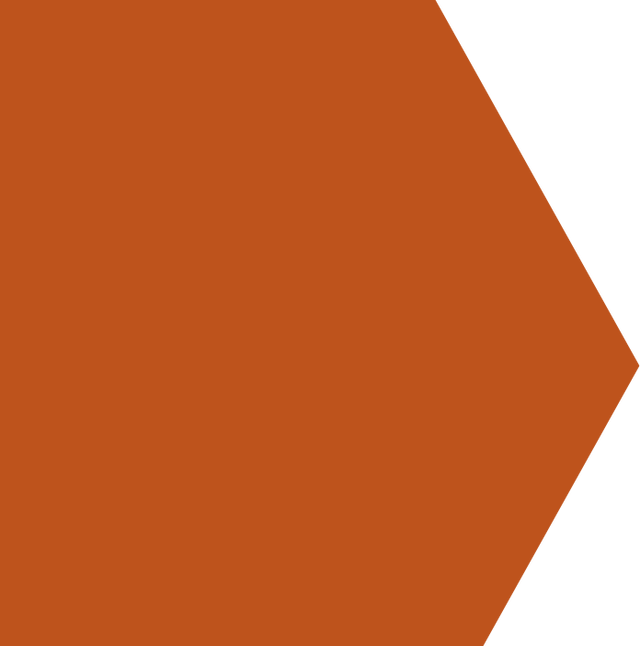
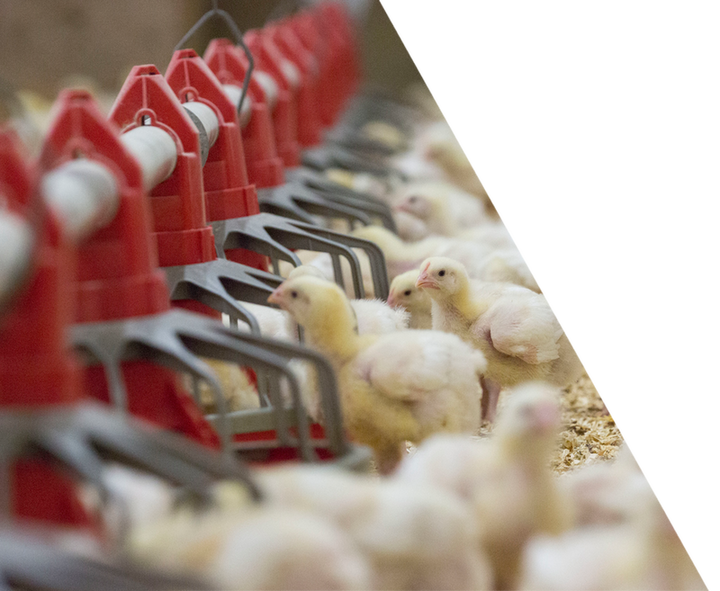
Decreased productivity: Finding the culprit
A commitment to get to the root of a particular livestock management issue is what often differentiates the Alltech customer support approach.
With just one look at the laying flock, it became very clear to Nick Alt that something wasn’t right. After receiving a call from an organic egg producer in northeast Ohio who was experiencing production issues, he made the eight-hour trek from Wisconsin to assess the situation.
“The birds were very stressed,” said Nick. “Their hackle feathers were raised, some were losing feathers and starting to self-molt. But the strangest part of it all was the flock’s production levels.
“The birds’ food intake would drop, which was followed by a decrease in egg production,” he continued. “Everything would steady out again and then production would increase, which would be followed by another decrease in feed consumption and production.”
While the main hat Nick wears is as a poultry sales support specialist for Alltech, his dynamic career in genetics, egg production and nutrition has handed him a selection of headgear to put on when assessing an operation for issues and then finding solutions to fix them.
“The thing that really threw me was the decrease and increase in feed consumption and production levels — it didn’t make sense.”
After his initial walkthrough of the farm, Nick suspected the issues were driven by a mineral deficiency due to how stressed the birds were. He took feed samples from the producer’s two feed bins to be tested for mycotoxins using the Alltech 37+® mycotoxin analysis.
“The thing that really threw me was the decrease and increase in feed consumption and production levels — it didn’t make sense,” explained Nick. “When the 37+ results came back, it showed high levels of DON (deoxynivalenol) in samples taken in one area of one of the feed bins, but the rest of the feed tested fine. It turned out he was mixing feed from the contaminated feed bin with the clean feed bin, which explained the swing in production.”
To find the root cause of the problem, Nick made the journey back to northeast Ohio, but this time it was to visit the feed mill supplying the farm.
“When testing for mycotoxins, nothing can replace the broad spectrum and sensitivity of the 37+ test,” said Nick. “However, when I need to find out right away if there is an issue, the Alltech® RAPIREAD™ system is a very good tool to make immediate, on-the-spot management decisions while we wait for the more comprehensive 37+ results to be processed at the lab.”
Pinpointing the problem, and a solution
If Nick was a betting man, his money would have been on the oldest corn in storage from the 2016 harvest to be the mycotoxin culprit, but after running multiple samples through RAPIREAD, he found it to all be at acceptable levels.
“I suspected that the bad batch of feed came from the mill switching from old corn to this harvest’s new corn, but that wasn’t the case,” he explained. “After talking to a couple of people who work at the feed mill, they told me the auger was being cleaned out when the bad batch of feed was made. When I put those samples through RAPIREAD, it tested for 0.5 parts per million (ppm) of DON.”
Along with advising the feed mill to use Integral® OA, which reduces mycotoxin absorption within the animal, Nick also followed up with other poultry producers in the area receiving feed from the mill.
“It turns out there were four other layers experiencing issues off this bad batch of feed,” he said. “One in particular saw his birds peaking at a 96 percent production rate before dropping down to 92 percent. After Integral OA started showing up on the feed tag, his birds went back to a 95 percent production rate.”
It’s more than sales
For someone like Nick who has spent their entire career primarily in the layer industry, his role as a sales support specialist is much more than providing products to customers.
“Needs change from client to client, but the most important part of my job is visiting producers and discussing what their challenges are and to then help them find solutions,” he said. “If I can help them with Alltech products, then that’s what I suggest, but if I can’t, then I help them find the answer they need.
“These people trust us to help them make the right management decisions to run a profitable business, which is their livelihood,” added Nick. “This can be a little scary, but at the same time, it amplifies the need to provide the best possible service we can, no matter the situation.”