Summary
Having a robust quality system that works for your mill is the key to keeping customers, employees, and auditors happy. It greatly reduces the risk of mycotoxin contamination in the feed chain and helps keep your customers safe, and their animals, from other harmful contaminates.
For more information on controlling mycotoxins in your mill please contact your mycotoxin representative.
Equipment
Storage bins and equipment should be monitored and cleaned regularly.
These areas are often perfect environments for mycotoxins to be produced and are often overlooked. Empty ingredient storage bins on a regular basis and clean grain storage bins as often as possible.
Remove any molded grains from the bin and fix holes and leaks. Have the rest of the mill on a regular cleaning schedule to ensure the mill is clean and presentable.
Monitoring
Mycotoxin monitoring has become more important as new information on the effects they have on different species have been discovered. Have a testing schedule in place that represents the feed being milled. Watch for mycotoxin reports such as the Harvest Analysis that Alltech provides.
These reports provide an overview of the mycotoxin contamination that may be present in the different regions that you are buying grain from. Have a tool to analyze ingredients ready at the mill. Neogen's Raptor is a great option that is user friendly and provides accurate information in a timely manner. Even with a Raptor at the mill, samples should be sent periodically to an outside lab, such as Alltech's 37+ lab, to receive a more detailed mycotoxin analysis of the ingredients coming to the mill.
Packaging
Bagged ingredients are often overlooked but should be included in your quality procedures. Check for torn bags and that ingredients have not changed before using.
Liquids can be difficult to monitor because of the enclosed nature of the shipment containers. Having a trusted supplier ensures a quality product is being delivered. Take samples from the containers when the shipment is unloaded to examine the quality of the product.
Receiving
At receiving, using a trusted supplier is critical to ensure a consistent quality of the products being delivered. Documentation at receiving, such as a supplier guarantee or previous load hauled form, is important to keep suppliers aware of your requirement for ingredients.
Physically inspecting ingredients before unloading for foreign material, smell, and off color should also be included in the process of receiving. Take a proper sample using proven techniques to produce a homogeneous sample.
Importance
Mills often see mycotoxins as a problem coming from suppliers bringing contaminated ingredients in that are commonly used in the feed manufacturing process. While there is no question suppliers’ ingredients may be contaminated, there are other avenues mycotoxins can be introduced downstream from suppliers.
There are areas in mills such as storage equipment, legs, and drags that are ideal places for molds contaminating the feed mill and producing mycotoxins. Mycotoxins are not released until a mold is stressed, which can be caused by factors such as temperature, moisture, and the presence of other molds. Just because testing at receiving shows clean ingredients, it does not guarantee contamination cannot occur further within the system because of conditions inside the mill. To combat these issues, a suitable quality system is critical for mills to prevent a mycotoxin problem after receiving.
The importance of quality feed in mills
Alltech Mycotoxin Management
Author: Dr. Alexandra Weaver, Alltech Mycotoxin Management
When testing feedstuffs or complete rations for mycotoxins, the results are only as good as the sample. It is often the case that an estimation of mycotoxin content of an entire lot is based on a small sample. It is critical that samples are representative, so that conclusions drawn about the mycotoxin profile can be as accurate as possible. As such, proper sampling techniques should be followed to minimize variation and improve the accuracy of results.
The role of sample variance
Mycotoxin type and concentration will naturally vary within a feedstuff, resulting in some areas of high risk and others of little or no risk. Obtaining an adequate sample that represents both the highs and lows is key to reducing the variance in mycotoxin test results (Weaver et al., 2020). The consequence of high sample variance is the formation of inaccurate conclusions. If test results overestimate the risk, a feedstuff or feed may be rejected when it does not need to be. If test results are too low, the commodity is accepted when it could pose a health risk to the animal.
When considering the sources of variance, it is estimated that sampling variance may account for about 75% of the total variability in mycotoxin test results, sample preparation for about 16% and analytical procedure for only about 8% (Miraglia et al., 2005). Based on these numbers, it is clear that having a proper sampling program that minimizes variance is key to obtaining accurate mycotoxin test results.
Sampling method for grains
To reduce sample variance, multiple small subsamples should be taken throughout a lot (Weaver et al., 2020). Collection of these samples should be spread out evenly throughout the lot. The number of collected subsamples depends on various factors, including matrix type, lot size and if it is moving or static. The European Commission (2006) states:
Lot size | Number of incremental samples | Final aggregate weight |
< 50 tonnes | 10–100 | 1–10 kg |
> 50 tonnes | Minimum of 100 | 10 kg |
Closed system (silo, ship, etc.) | Sample at least 10% of total lot |
The most effective sampling method is automatic sampling from a moving stream, where small samples are removed at standard intervals throughout the lot’s entire movement. Automatic sampling was shown by Mallmann et al. (2014) to reduce sampling variance by 5.6 times and total variance by 3.9 times. If automatic sampling is not available, probe sampling can be used. Multiple probe samples should be collected throughout the entire lot in order to obtain the most accurate representation of mycotoxin contamination.
Sampling method for forages
When sampling silages, it is important to ensure safety when accessing a bunker. Subsamples should be collected from at least 8–10 locations throughout a freshly faced silage clamp, ideally using a hand drill. Mix the subsamples to form a well-blended composite sample. Once fully mixed, quarter the sample to obtain an appropriate final sample size. If round or square bales need to be sampled, collect subsamples using a hand drill or hay probe from 5–10 bales. Obtain a well-mixed composite sample, and quarter as necessary.
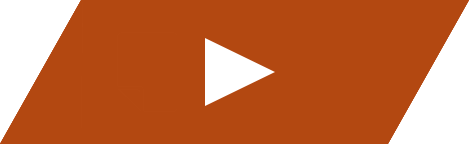
Preparing the sample and submitting for mycotoxin analysis
Once subsamples are obtained, they should be well mixed to get a homogenous composite sample. This composite sample will likely need to be further subdivided to reach an acceptable final sample size. To reduce sample size, follow the quartering method. Place the sample in an airtight bag and send it for testing. Samples can be analyzed for mycotoxins in several different ways, including using rapid test kits (Alltech® RAPIREAD™) or by LC-MS/MS (Alltech 37+® mycotoxin analysis).
The importance of proper sampling when assessing mycotoxins
Obtaining a representative sample is critical for accurately assessing mycotoxin risk. If that sample does not correctly represent the lot, then the risk in that feedstuff or feed may be classified incorrectly and result in either economic loss for the producer or health consequence for the animal. Mycotoxins can play a significant role in animal performance, health and productivity. As such, an accurate assessment of mycotoxin risk is necessary in order to develop a successful mycotoxin management program.
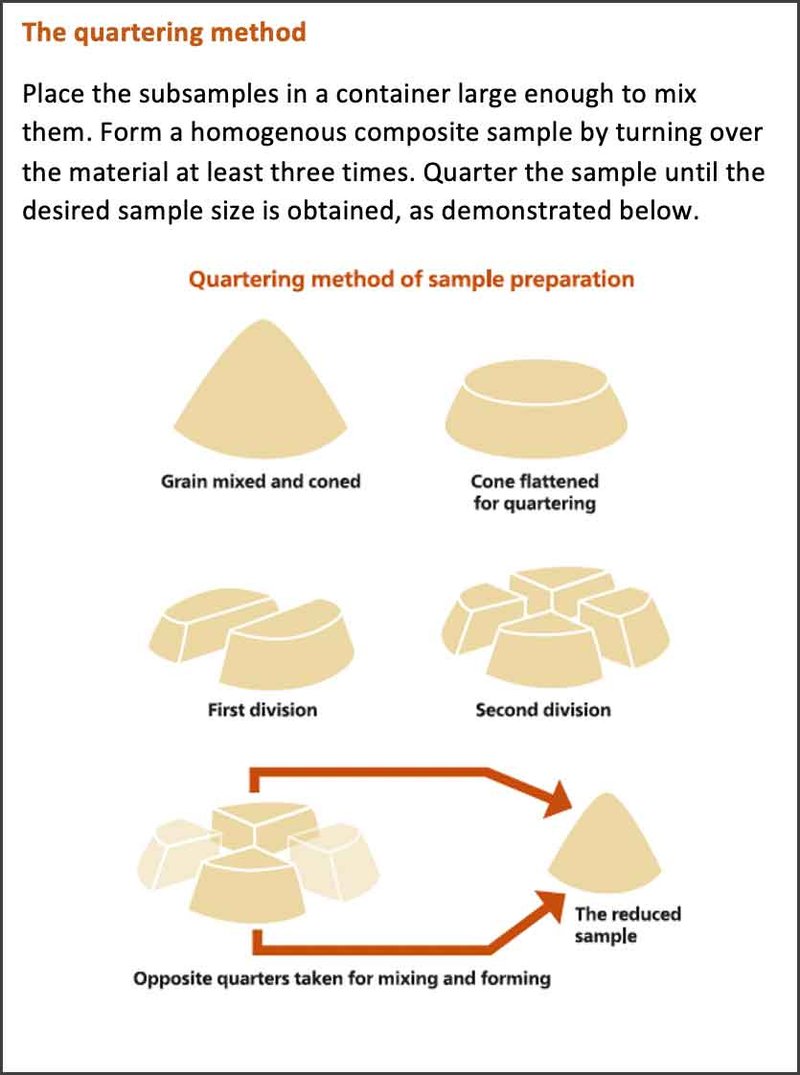
Does yeast cell wall interact with materials other than mycotoxins?
The composition of the yeast cell wall is such that it does not interact with other components in the diet, such as vitamins, minerals or antibiotics.
Internal work established that sorption capabilities were very limited toward vitamins and trace elements due to a lack of compatibility between the molecular structures of those nutrients and the site of interaction on the beta-D-glucans, the type of interaction necessary to the adsorption process, the differences in chemistry with nutrients, the differences in concentration and bioavailability of nutrients or because of the interaction balance.
As a result, animal nutrition is not affected by the use of yeast cell wall extract.