
How technology can help prepare
for new crop STORAGE
Author: Josh Teulker, Global Feedmill Specialist, Alltech Mycotoxin Management
and Dr. Wilmer Pacheco, Feed Mill Extension Specialist, Auburn University
Over the next couple of months, mills will be preparing for harvest, with a long to-do-list to complete before the new grain arrives.
Cleaning and treating bins, ensuring aeration is working properly, having a sampling plan and understanding storage conditions are all topics to prepare for before the new crops arrive at the mills this season.
Each step is important to ensure grains at the facility are correctly stored, and the integrity of the grain is kept after receiving it.
Bin cleaning and treating
Cleaning a grain bin can be labor-intensive and dangerous and, thus, safety must be considered at all times. Technology has improved on grain cleaning equipment, allowing zero entry into the bin for cleaning. A bin sweep that allows zero entry to clean the vast majority of the grains with very little labor is an investment any mill should consider. These sweeps speed up the cleaning process and reduce the risk of employees entering bins for cleaning. Even after the sweep has made its rounds, there might be a need to enter and manually remove grains from the corners. This can be done with a shovel, or a quicker option is a grain vacuum. Obviously, vacuums are substantially more expensive than a good shovel, but they are a valuable tool for larger grain facilities, especially when quick turnaround is needed. Discard any grains that may be high in foreign material or molded that are left after sweeping; they are not worth the risk of feeding and losing production efficiency or jeopardizing animal health.
Once the bin has been swept, inspect for leaks. A sign of a leak is often grain sticking to the side wall or an area where mold has grown. These spots are usually obvious, with light coming through the hole into the dark bin. Clean any areas of grain buildup and patch the hole to ensure the new crop grains are stored where outside moisture cannot get into the bin.
Insects can be an overlooked problem in grain storage, specifically the common maize weevil. Corn is the perfect environment for the weevil, which makes its way into the seed and lays an egg in the kernel. The juvenile weevil then bores through the kernel, essentially leaving nothing but grain dust and the kernel shell. Inspect bins to ensure they are free of pests before filling with new grain. There are many products on the market for treating bins for insects. Find the best product that will work for your situation and follow the directions from the manufacturer.
With the bin empty and clean, check to ensure bin fans and aeration systems are working properly. Each fan should run smoothly, and the path of the air should be free of debris. The aeration system is a key tool to keep grains in storage for a long period of time. Mismanaging aeration will be detrimental to the grains and very costly to the mill.
Sampling and quality control
Correct sampling can help the feed mill manager or the quality control supervisor reject grains that do not meet nutritional or physical specifications or pose chemical or biological hazards. Since cereal grains represent around 60% of total diet composition, sampling helps nutritionists evaluate their nutrient profile, update nutrients’ matrix in the formulation program and produce feeds that comply with the nutrient specifications for different animals depending on their age, type and phase of production. Near infrared (NIR) spectroscopy can also be a tool to evaluate the quality of incoming grains.
For mycotoxin testing, tools like Alltech 37+ and Alltech RAPIREAD provide feed mills and producers with an effective way to analyse the mycotoxin risk in incoming grains, allowing for ingredient segregation if necessary or the further use of mycotoxin binding products in the feed production process.
Figure 1. Sample patterns for hopper bottom and dump trailer trucks
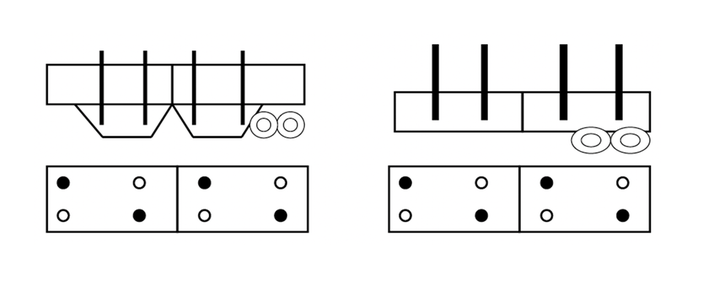
Storage conditions
In recent years, the industry has implemented technologies to monitor the quality of grains during storage. Grain losses during storage typically occur through mold spoilage and insect infestation. Since mold and insect growth cause increases in heat and CO2, thermocouples and CO2 sensors can be used to monitor the condition of the stored grains.
Thermocouples detect changes in temperature within a few meters from the sensors and CO2 sensors can detect changes in CO2 as it moves with air currents. Normally, the level of CO2 for good-condition grains is approximately 500 ppm. If readings are higher than 1,400 ppm, grain should be monitored, as it can indicate mold growth, possible mycotoxin production and/or insect infestation.
Both tools can be used to make decisions regarding grain aeration to reduce hot spots, remove moisture and eliminate temperature gradients inside the silos.
Conclusion
A lot of thought and effort must be put into the mill before new grains begin to flow in. Taking the time to ensure all the boxes are checked will save you time and money on the bottom line.
Technology has made the tasks much easier and streamlined. However, each day may see a new challenge in storage. Mills must physically inspect bins to ensure the technology is properly functioning. A robot or sensor cannot replace the human eye.
Make it a habit to physically monitor your storage to ensure quality grain for feed manufacturing.

How technology can
help prepare for new crop
Author: Josh Teulker, Global Feedmill Specialist, Alltech Mycotoxin Management
and Dr. Wilmer Pacheco, Feed Mill Extension Specialist, Auburn University
Over the next couple of months, mills will be preparing for harvest, with a long to-do-list to complete before the new grain arrives.
Cleaning and treating bins, ensuring aeration is working properly, having a sampling plan and understanding storage conditions are all topics to prepare for before the new crops arrive at the mills this season.
Each step is important to ensure grains at the facility are correctly stored, and the integrity of the grain is kept after receiving it.
Bin cleaning and treating
Cleaning a grain bin can be labor-intensive and dangerous and, thus, safety must be considered at all times. Technology has improved on grain cleaning equipment, allowing zero entry into the bin for cleaning. A bin sweep that allows zero entry to clean the vast majority of the grains with very little labor is an investment any mill should consider. These sweeps speed up the cleaning process and reduce the risk of employees entering bins for cleaning. Even after the sweep has made its rounds, there might be a need to enter and manually remove grains from the corners. This can be done with a shovel, or a quicker option is a grain vacuum. Obviously, vacuums are substantially more expensive than a good shovel, but they are a valuable tool for larger grain facilities, especially when quick turnaround is needed. Discard any grains that may be high in foreign material or molded that are left after sweeping; they are not worth the risk of feeding and losing production efficiency or jeopardizing animal health.
Once the bin has been swept, inspect for leaks. A sign of a leak is often grain sticking to the side wall or an area where mold has grown. These spots are usually obvious, with light coming through the hole into the dark bin. Clean any areas of grain buildup and patch the hole to ensure the new crop grains are stored where outside moisture cannot get into the bin.
Insects can be an overlooked problem in grain storage, specifically the common maize weevil. Corn is the perfect environment for the weevil, which makes its way into the seed and lays an egg in the kernel. The juvenile weevil then bores through the kernel, essentially leaving nothing but grain dust and the kernel shell. Inspect bins to ensure they are free of pests before filling with new grain. There are many products on the market for treating bins for insects. Find the best product that will work for your situation and follow the directions from the manufacturer.
With the bin empty and clean, check to ensure bin fans and aeration systems are working properly. Each fan should run smoothly, and the path of the air should be free of debris. The aeration system is a key tool to keep grains in storage for a long period of time. Mismanaging aeration will be detrimental to the grains and very costly to the mill.
Sampling and quality control
Proper grain sampling is essential to evaluate their quality and ensure they are in a condition suitable for storage. The quality of the grains cannot be improved at the feed mill, and poor-quality or high-moisture grains are more difficult to manage and prone to mold growth. Sampling and evaluating physical characteristics of incoming grains, such as color, odor, moisture, foreign material and insect infestation, and mycotoxins before unloading are key to producing high-quality feeds. Prior to receiving, grains should be sampled following the pattern shown in Figure 1, or at 5–10 evenly spaced grab samples during the unloading process.
Correct sampling can help the feed mill manager or the quality control supervisor reject grains that do not meet nutritional or physical specifications or pose chemical or biological hazards. Since cereal grains represent around 60% of total diet composition, sampling helps nutritionists evaluate their nutrient profile, update nutrients’ matrix in the formulation program and produce feeds that comply with the nutrient specifications for different animals depending on their age, type and phase of production. Near infrared (NIR) spectroscopy can also be a tool to evaluate the quality of incoming grains.
Figure 1. Sample patterns for hopper bottom and dump trailer trucks
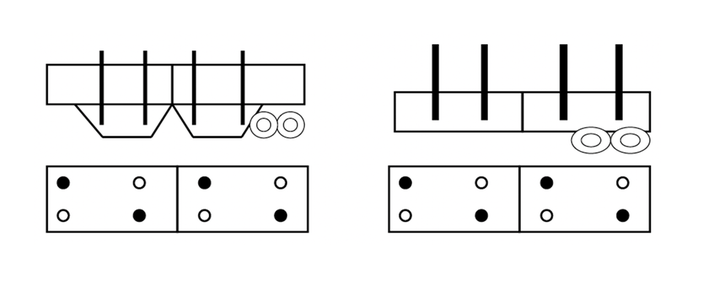
Storage conditions
In recent years, the industry has implemented technologies to monitor the quality of grains during storage. Grain losses during storage typically occur through mold spoilage and insect infestation. Since mold and insect growth cause increases in heat and CO2, thermocouples and CO2 sensors can be used to monitor the condition of the stored grains.
Thermocouples detect changes in temperature within a few meters from the sensors and CO2 sensors can detect changes in CO2 as it moves with air currents. Normally, the level of CO2 for good-condition grains is approximately 500 ppm. If readings are higher than 1,400 ppm, grain should be monitored, as it can indicate mold growth, possible mycotoxin production and/or insect infestation.
Both tools can be used to make decisions regarding grain aeration to reduce hot spots, remove moisture and eliminate temperature gradients inside the silos.
Conclusion
A lot of thought and effort must be put into the mill before new grains begin to flow in. Taking the time to ensure all the boxes are checked will save you time and money on the bottom line.
Technology has made the tasks much easier and streamlined. However, each day may see a new challenge in storage. Mills must physically inspect bins to ensure the technology is properly functioning. A robot or sensor cannot replace the human eye.
Make it a habit to physically monitor your storage to ensure quality grain for feed manufacturing.
Weather

How technology can
help prepare for new crop
Author: Josh Teulker, Global Feedmill Specialist, Alltech Mycotoxin Management and Dr. Wilmer Pacheco, Feed Mill Extension Specialist, Auburn University
Over the next couple of months, mills will be preparing for harvest, with a long to-do-list to complete before the new grain arrives.
Cleaning and treating bins, ensuring aeration is working properly, having a sampling plan and understanding storage conditions are all topics to prepare for before the new crops arrive at the mills this season.
Each step is important to ensure grains at the facility are correctly stored, and the integrity of the grain is kept after receiving it.
Bin cleaning and treating
Cleaning a grain bin can be labor-intensive and dangerous and, thus, safety must be considered at all times. Technology has improved on grain cleaning equipment, allowing zero entry into the bin for cleaning. A bin sweep that allows zero entry to clean the vast majority of the grains with very little labor is an investment any mill should consider. These sweeps speed up the cleaning process and reduce the risk of employees entering bins for cleaning. Even after the sweep has made its rounds, there might be a need to enter and manually remove grains from the corners. This can be done with a shovel, or a quicker option is a grain vacuum. Obviously, vacuums are substantially more expensive than a good shovel, but they are a valuable tool for larger grain facilities, especially when quick turnaround is needed. Discard any grains that may be high in foreign material or molded that are left after sweeping; they are not worth the risk of feeding and losing production efficiency or jeopardizing animal health.
Once the bin has been swept, inspect for leaks. A sign of a leak is often grain sticking to the side wall or an area where mold has grown. These spots are usually obvious, with light coming through the hole into the dark bin. Clean any areas of grain buildup and patch the hole to ensure the new crop grains are stored where outside moisture cannot get into the bin.
Insects can be an overlooked problem in grain storage, specifically the common maize weevil. Corn is the perfect environment for the weevil, which makes its way into the seed and lays an egg in the kernel. The juvenile weevil then bores through the kernel, essentially leaving nothing but grain dust and the kernel shell. Inspect bins to ensure they are free of pests before filling with new grain. There are many products on the market for treating bins for insects. Find the best product that will work for your situation and follow the directions from the manufacturer.
With the bin empty and clean, check to ensure bin fans and aeration systems are working properly. Each fan should run smoothly, and the path of the air should be free of debris. The aeration system is a key tool to keep grains in storage for a long period of time. Mismanaging aeration will be detrimental to the grains and very costly to the mill.
Sampling and quality control
Proper grain sampling is essential to evaluate their quality and ensure they are in a condition suitable for storage. The quality of the grains cannot be improved at the feed mill, and poor-quality or high-moisture grains are more difficult to manage and prone to mold growth. Sampling and evaluating physical characteristics of incoming grains, such as color, odor, moisture, foreign material and insect infestation, and mycotoxins before unloading are key to producing high-quality feeds. Prior to receiving, grains should be sampled following the pattern shown in Figure 1, or at 5–10 evenly spaced grab samples during the unloading process.
Correct sampling can help the feed mill manager or the quality control supervisor reject grains that do not meet nutritional or physical specifications or pose chemical or biological hazards. Since cereal grains represent around 60% of total diet composition, sampling helps nutritionists evaluate their nutrient profile, update nutrients’ matrix in the formulation program and produce feeds that comply with the nutrient specifications for different animals depending on their age, type and phase of production. Near infrared (NIR) spectroscopy can also be a tool to evaluate the quality of incoming grains.
Figure 1. Sample patterns for hopper bottom and dump trailer trucks
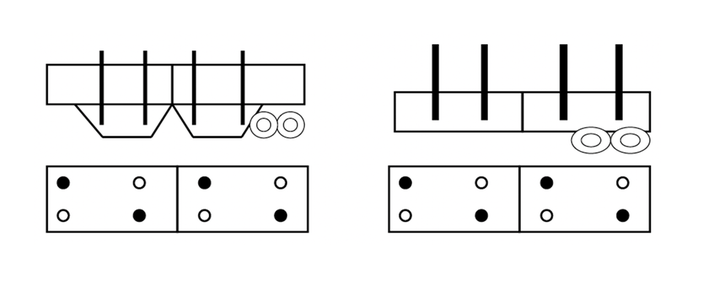
Storage conditions
In recent years, the industry has implemented technologies to monitor the quality of grains during storage. Grain losses during storage typically occur through mold spoilage and insect infestation. Since mold and insect growth cause increases in heat and CO2, thermocouples and CO2 sensors can be used to monitor the condition of the stored grains.
Thermocouples detect changes in temperature within a few meters from the sensors and CO2 sensors can detect changes in CO2 as it moves with air currents. Normally, the level of CO2 for good-condition grains is approximately 500 ppm. If readings are higher than 1,400 ppm, grain should be monitored, as it can indicate mold growth, possible mycotoxin production and/or insect infestation.
Both tools can be used to make decisions regarding grain aeration to reduce hot spots, remove moisture and eliminate temperature gradients inside the silos.
Conclusion
A lot of thought and effort must be put into the mill before new grains begin to flow in. Taking the time to ensure all the boxes are checked will save you time and money on the bottom line.
Technology has made the tasks much easier and streamlined. However, each day may see a new challenge in storage. Mills must physically inspect bins to ensure the technology is properly functioning. A robot or sensor cannot replace the human eye.
Make it a habit to physically monitor your storage to ensure quality grain for feed manufacturing.